Restoration of a Millers Falls Boring Machine - Part 1
The Machine
Timber framers who prefer hand methods often use a manual boring machine for clearing the bulk of material from a mortise before refining its walls with a chisel or a slick. Figure 1 shows the author using a Millers Falls boring machine for this purpose in a Heartwood School timber framing course. This article describes the author’s experience in restoring a similar machine, which is shown in its eBay listing in Figure 2.
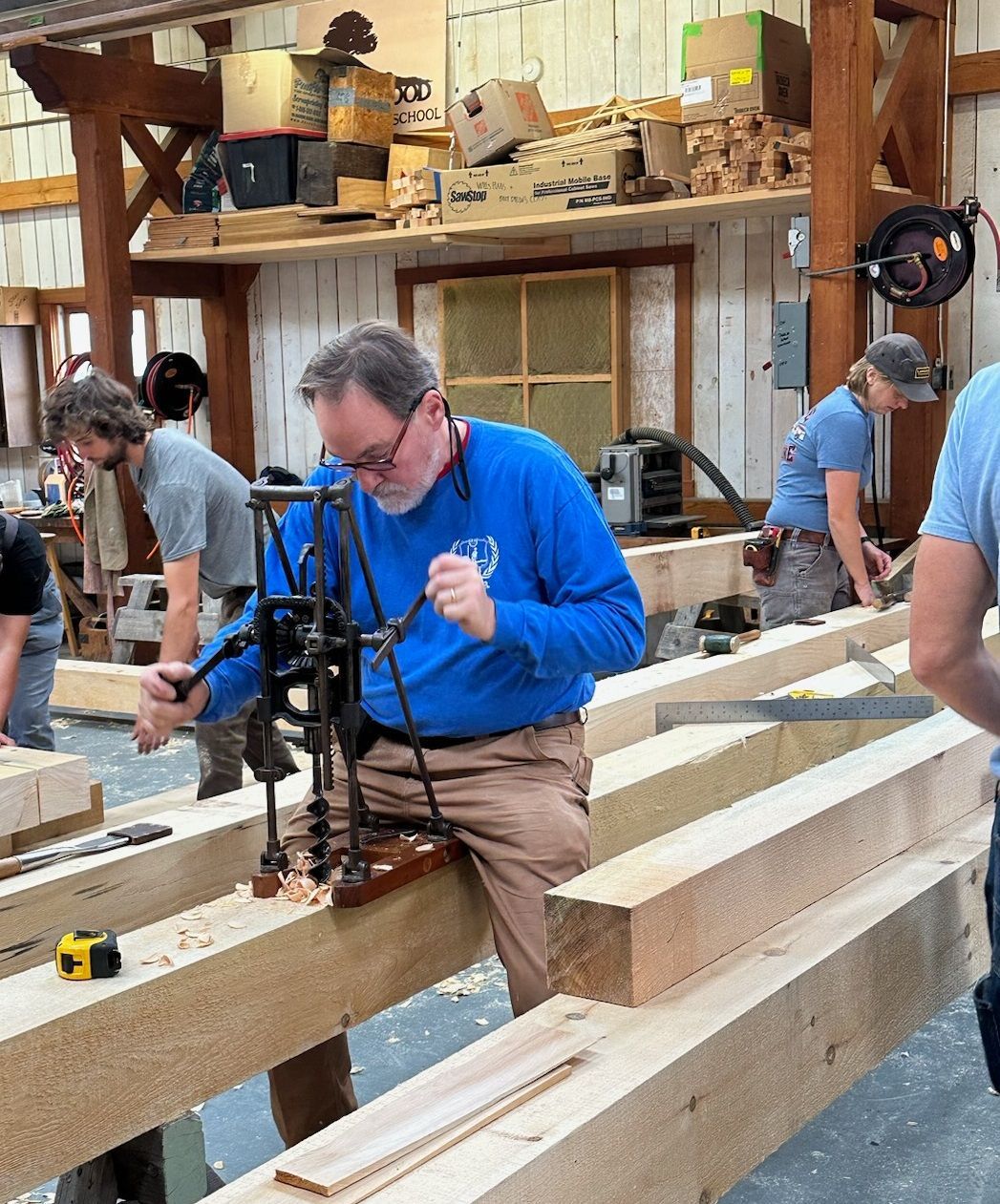
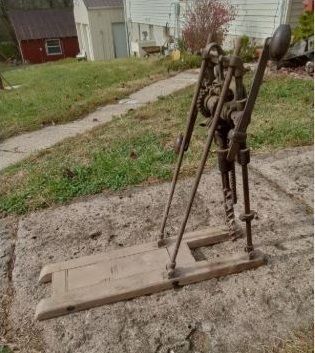
A Brief History of Boring Machines in Timber Framing
These machines bore holes perpendicular to a timber’s surface, while some machines can bore at other angles as well. Some machines, such as those made by Millers Falls, have a rack and pinion mechanism to extract the drill bit. It is not known when the boring machine (a.k.a. beam drill, beam auger) was invented, although the first patent is by J. Beckwith in 1830. Boring machines were made by Millers Falls, the James Swan Co., the Buckeye Manufacturing Company, and Lambert Brothers among perhaps others. By 1886, Millers Falls claimed they had perfected the machine in the Scientific American¹, and the machines appeared in Millers Falls catalogs starting in 1887 and continuing through 1929² although people with considerable experience in rebuilding these machines have claimed in online posts that Millers Falls manufactured boring machines into the 1930s and possibly the 1940s. The Millers Falls No.145 boring machine with a wood base was listed at a price of $9.25 (without augers) in the 1915 catalog (see Figure 3), which is equivalent with approximately $288 in 2024 dollars according to a Federal Reserve inflation calculator. It is interesting that the demand for these vintage machines is such that any machine in good or salvageable condition sells for considerably more than the original price adjusted for inflation.
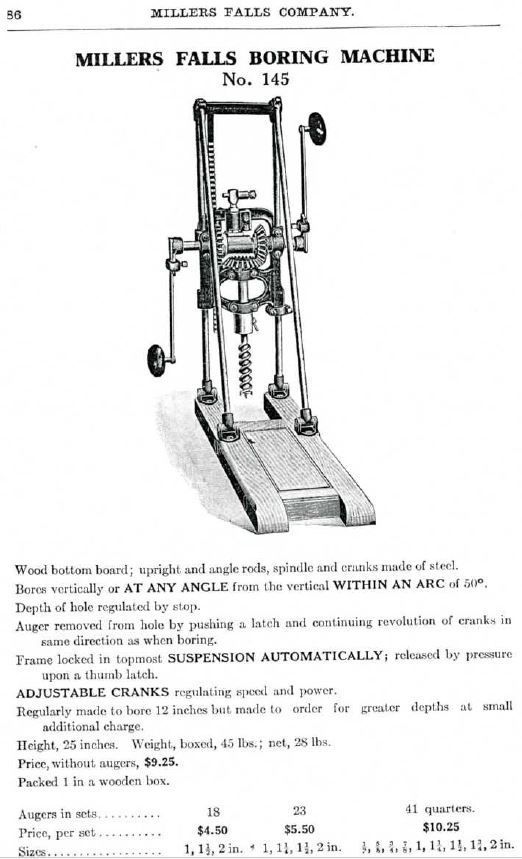
Of the timber framers who have expressed a preference for boring machines to the author, all prefer Millers Falls machines. Many in online forums also express a preference for Millers Falls machines, whereas the author has never seen a preference expressed for another make. Among the advantages of Millers Falls machines, besides the bit extraction mechanism, is that the boring frame is supported by four steel rods rather than a wooden frame that other machines rely on either entirely or in part. The Millers Falls name was cast into machines that they manufactured although some boring machines, such as the one purchased by the author, are identical to Millers Falls machines but have no markings, neither the Millers Falls name nor any other maker’s mark.
It is still possible, however, and even likely that unmarked boring machines like the author’s machine were made by Millers Falls given that the trademarks do not always indicate which company made the tool. Tool manufacturers have for a long time made tools to be sold under other companies’ tradenames, such as Sears’ Craftsman tools and
Montgomery Wards’ Master Quality tools. It seems that none of the
Craftsman and Master Quality tools were made by Sears and Montgomery Wards, respectively. For example, Craftsman planes are known to have been manufactured by Millers Falls, Sargent, and Stanley³,⁴,⁵,⁶,⁷,⁸,⁹. Even Stanley subcontracted the manufacture of planes to Sargent in Stanley’s early years of selling planes¹⁰. Sears and Montgomery Wards also had brand names for lesser quality tool lines; Fulton, Dunlap, and Merit for Sears and Lakeside for Montgomery Wards, which were also made by other companies.
Eggbeater drill collectors have similarly noted in online discussions that they have identical drills that are branded differently, which might indicate that a single manufacturer produced the same drill design for multiple brands. Additionally, a person associated with the Museum of Our Industrial Heritage indicated that companies did make tools for other companies in the era in which boring machines were produced, as is also the case today¹¹.
Conversely, the lack of a brand name in a tool casting doesn’t necessarily indicate that a tool was not made by a well-known toolmaker. Tools made to be wholesaled to many distributors or retailers might have been unbranded or branded in a less durable manner than within a casting: producing tools in this manner obviates the investment for dedicated casting molds or other tooling for each particular brand so that distribution could be more profitable even when a customer purchased a small number of units. For example, some planes made by Millers Falls and sold by Sears were
marked with an ink stamp. Ink stamps and decals, even if they were applied to the tools, would likely succumb to hard use over many years. It is possible, under this scenario, that Millers Falls would produce a boring machine that, today, bears no evidence of its maker. Some also suggest that earlier Millers Falls boring machines may not have been marked with the Millers Falls’ name.
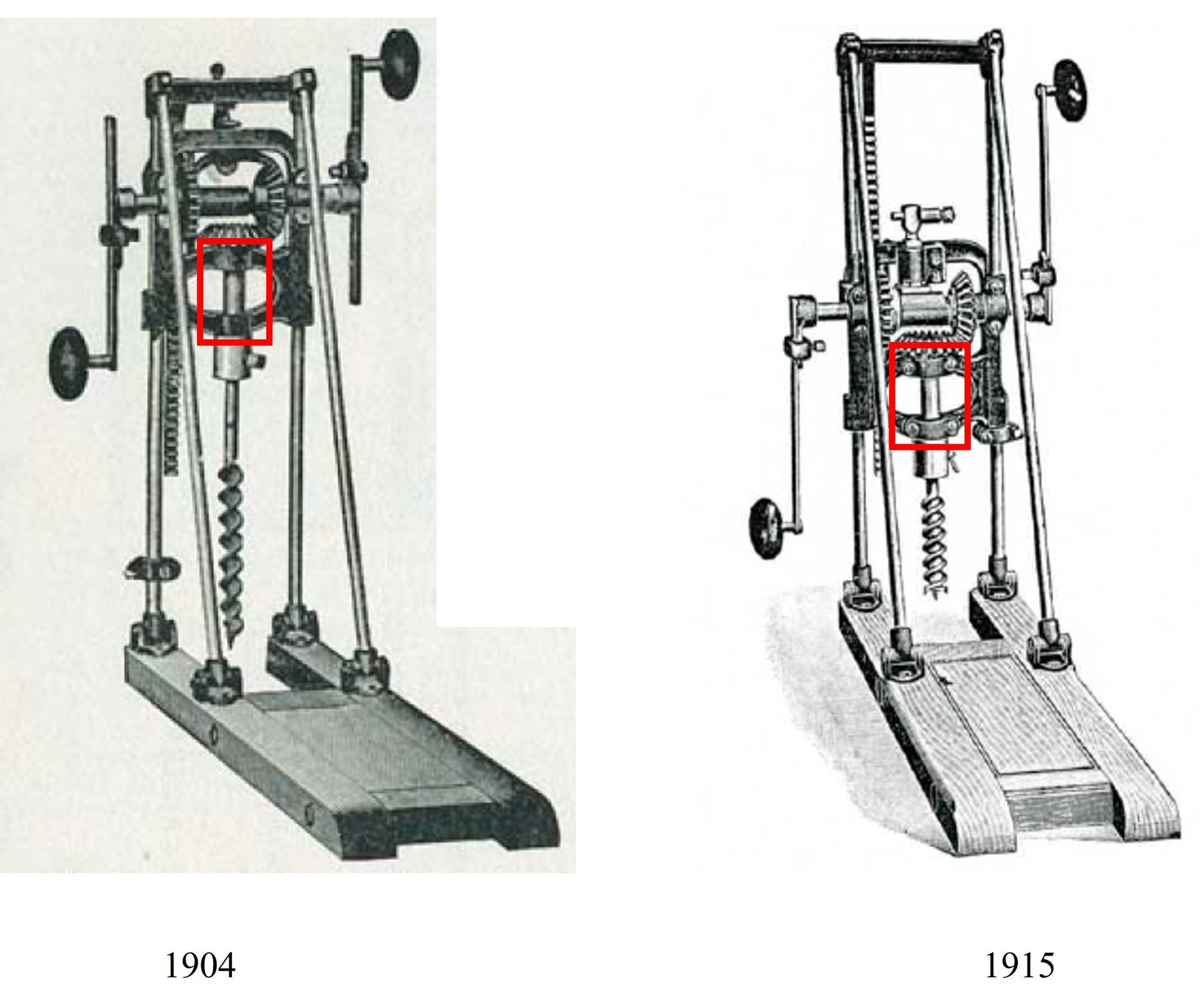
Although counterarguments are possible for the unmarked boring machines being produced by a company other than Millers Falls, as would be the case if another company made a “knock off” version, the author presumes that their machine was indeed made by Millers Falls.
Boring machine designs vary among makers, and even Millers Falls’ design varied over the years with updates to the retraction mechanism and the journal bushings for the boring shaft. For example, both sides of the journal bushing were part of an integral cast in 1904 but, by 1915, one side of the bushing housing was removable, as shown in Figure 4. Nonetheless, the restoration methods described in subsequent postings would still apply to any machine. That said, the author does not claim that the restoration approach described here is best, but the description of methods, materials, and tools used will hopefully be helpful to those pursuing similar projects.
- Scientific American (Architects and Building Edition), The Millers Falls Boring Machine, Volume 1, Issue 5, March 1886, p. 143.
- Communications with the curator, Al Shane, of the Museum of Our Industrial Heritage, Greenfield, MA on December 14, 2024.
- https://www.timetestedtools.net/2016/02/09/known-examples-of-planes-made-by-millers-falls-for-other-companies/
- https://industrialhistory.org/files/Fitzgerald_-_Millers_Falls_Planes-07092022.pdf
- https://www.facebook.com/photo/?fbid=650788678869540&set=a.391410194807391
- https://www.timetestedtools.net/2016/02/26/craftsman-hand-plane-model-number-comparison/#google_vignette
- https://www.justtheplanefacts.com/
- https://www.justtheplanefacts.com/assorted-rebrand-planes#:~:text=An%20ink%20stamp%20was%20applied,sell%20a%20jack%20plane%20version.
- https://aplanelife.us/plane-galleries#:~:text=Produced%20by%20Millers%20Falls%20under,a%20factory%20could%20profitably%20produce.
- https://www.youtube.com/watch?v=xxEBuZNlWeM
- Communications with Marc Fournier via email, December 15, 2024.
If you have any inquiries or comments, you can contact the author at jrbrad314159@gmail.com
If you are interested in using historic tools, come learn to use a boring machine and more with us! Our Timber Framing courses focus on traditional methods using high quality historic and modern tools.
share this
Related Articles
Related Articles
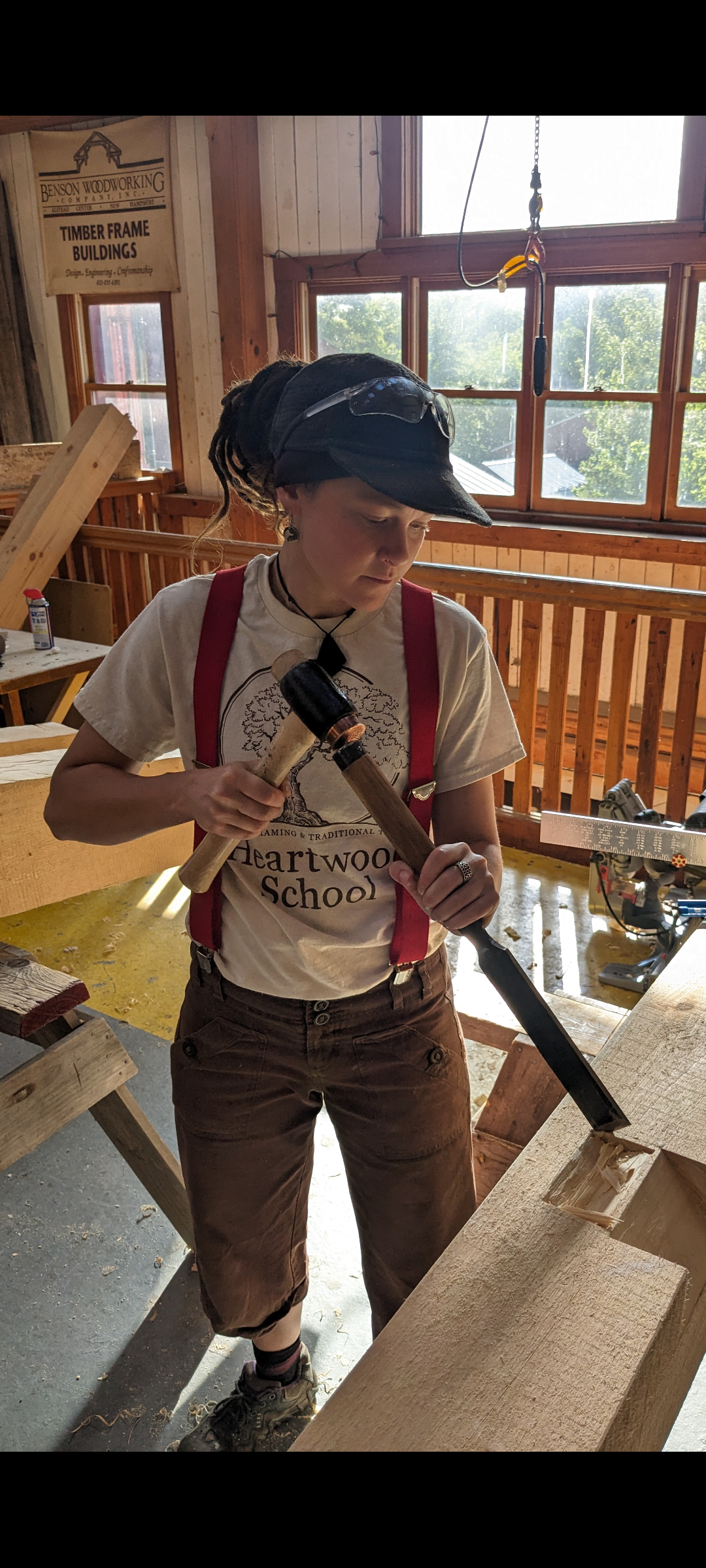